DTF Printing Process Guide
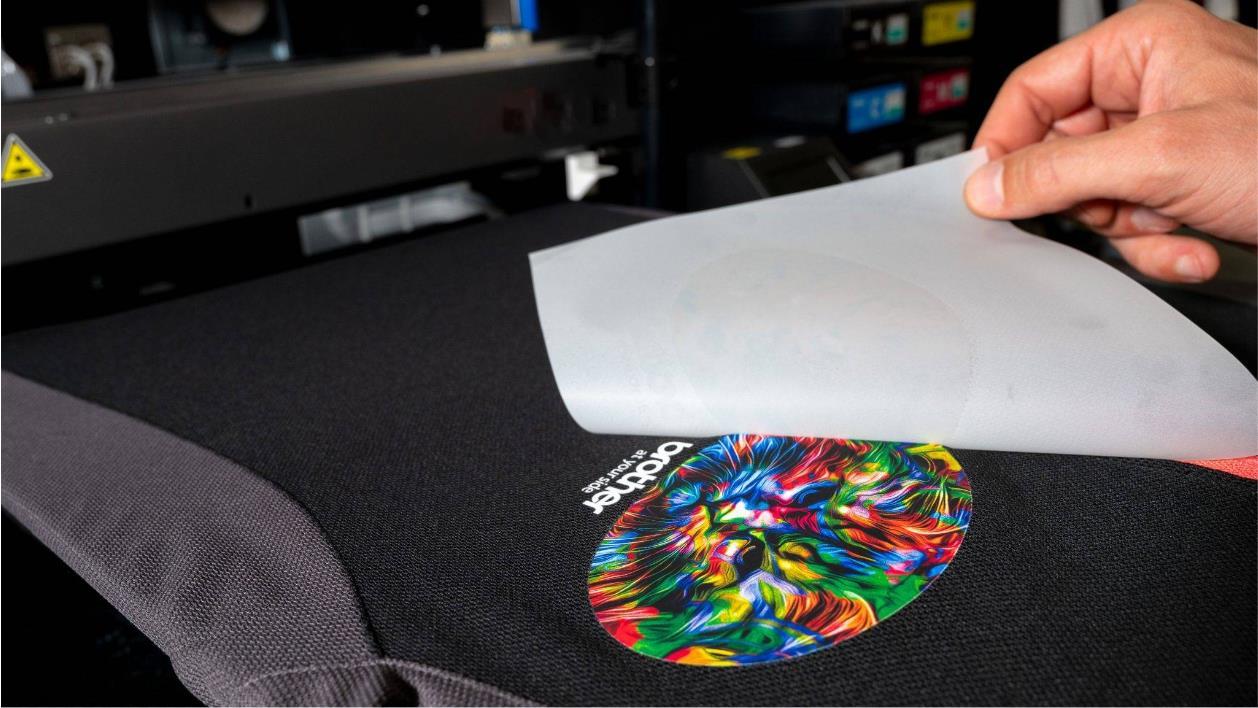
The digital textile printing industry has seen rapid growth over the past decade as more and more users turn to the digitization of textile printing. The use of digital printers enables one to instill ease, simplicity, fabric performance, consistency, and most importantly, a variety of colors in textiles, making the entire process overall reliable and cost-effective. Digitally printed textiles cover several processes. In this article, we will mainly discuss the DTF printing process flow.
Popular Textile Printing Processes:
1. Digital sublimation printing
2. Digital textile printing
3. Direct-to-film printing
What is DTF Printing?
The DTF process is as simple as its name suggests - print on film and transfer directly to fabric. The most prominent factor that makes this process worthwhile for more people is the freedom to choose almost any fabric. Whether it's polyester, cotton, silk, or synthetic fibers like rayon or cotton terry, the DTF printing process works its magic on them.
Advantages of DTF Printing
1. Suitable for almost all types of fabrics
2. No preprocessing is required
3. The fabrics thus designed exhibit good washing properties.
4. The fabric has a very slight feel to the touch
5. The process is faster and simpler compared to DTG printing
Prerequisites for DTF Printing
The requirements of DTF printing do not require a large investment by the user. Whether someone who is currently working on one of the above-mentioned textile digital printing processes and wants to switch to DTF printing as a business extension or someone who wants to get into digital textile printing starting with DTF, must invest in the following:
1. DTF Printer
These printers are often called DTF printers. Most of these printers are basic 6-color ink cartridge printers. The reason for choosing this series of printers is that these printers use 6 colors. This facilitates operation as CMYK DTF ink can go into standard CMYK ink tanks, while the printer's LC and LM ink tanks can be filled with white DTF ink. In addition, the rollers used to slide the pages have been removed to prevent "liners" from appearing on the white layer printed on the DTF film.
2. Films
PET film is used in the DTF printing process. These films are different from those used in screen printing. They have a thickness of about 0.75mm and better transmission characteristics. In the language of the market, these are often referred to as DTF transfer films. DTF film is available in cut sheets (available for small-scale use) and rolls (for commercial settings). Another classification of PET film is based on the type of peeling performed after transfer. Depending on the temperature, the film is a hot-peel or cold-peel film
3. Software
The software is an essential part of the process. The printing properties, the color performance of the inks, and the final print performance on the fabric after transfer are greatly influenced by the software. For DTF, specialized RIP software is required to handle CMYK and white. Color profiles, ink volumes, drop size, and other factors that help optimize print results are all controlled by the DTF printing software.
DTF printing powder is white and acts as a binding material that binds the colored pigments in the print to the fibers in the fabric. There are different grades of DTF hot melt powder, measured in microns. The appropriate grade should be selected according to the requirements.
5. DTF Printing Ink
These are specially designed-pigment inks available in cyan, magenta, yellow, black, and white. White ink is a special component that lays the base of the printed white on the film and onto which the colored designs are printed.
6. Automatic Powder Shaker
An automatic powder shaker is used in commercial DTF settings to evenly apply powder and remove excess powder.
7. Curing Oven
A curing oven is a small industrial oven used to melt hot melt powder coated on the transfer film. Alternatively, a heat press can also be used to do this but should be used in non-contact mode.
8. Heat Press Machine
The heat press is mainly used to transfer the image printed on the film to the fabric. It can also be used to heat hot melt powder on DTF film. The method for doing this is explained in the procedure detailed below.
Basic Steps for Direct-To-Film Printing
Step 1 - Print on Film
Insert PET film into the printer tray instead of plain paper. First, print the entire image in white on PET film. After this, print the desired image on the white image layer using the appropriate color settings in the printer. The important thing to remember is that the print on the film must be a mirror image of the actual image that needs to appear on the fabric.
Step 2 - Powder
This step is to apply the hot melt powder to the film printed with the image. When the ink is wet, the powder spreads evenly, and excess powder needs to be removed carefully. It is important to ensure that the powder is evenly distributed on the printed surface of the film.
A very common way to ensure this is to hold the short side of the film so that the long side is parallel to the floor (laterally) and pour the powder into the middle of the film from top to bottom so that it forms a mound about 1 inch thick In the center from top to bottom.
Pick up the film along with the powder and bend it slightly inward so that it forms a small U with the concave side facing you. Now gently shake the film from left to right to spread the powder slowly and evenly over the entire surface of the film. Alternatively, automated shakers available in commercial settings can be used.
Step 3 - Melt the Powder
As the name suggests, the powder is melted in this step. This can be done in a number of ways. The most common method is to heat the image-printed film and powder-coated film in a curing oven. If the curing oven is not available, place the film inside the heat press with the top of the press very close to the film, but do not touch it.
There should be about a 4 to 7 mm gap between the film and the heat-pressed top plate. A wire can be used to secure the top of the press so it doesn't close the film and leave the necessary gap. For best results, it is strongly recommended to follow the manufacturer's powder melting specifications. Depending on the powder and equipment, the heating time is generally 2 to 5 minutes and the temperature is around 160 to 170 degrees Celsius.
Step 4 - Pre-Pressing
This step includes pre-pressing the fabric before the film transfers the image. The fabric is kept in the heat press and pressed under heat for about 2 to 5 seconds. This is done to flatten the fabric and ensure that the fabric is dehumidified. Pre-pressing helps to properly transfer the image from the film to the fabric.
Step 5 - Transfer
This is the heart of the DTF printing process. The PET film with the image and melted powder is placed on the pre-pressed fabric in a heat press to have a strong bond between the film and the fabric. This process is also known as "curing". Curing takes place at a temperature ranging from 160 to 170 degrees Celsius for approximately 15 to 20 seconds. The film is now firmly attached to the fabric.
Step 6 - Cold Peel
The fabric and the film now attached to it must be cooled to room temperature before the film can be removed. Because hotmelt has amide-like properties, as it cools, it acts as a binder, holding the colored pigments in the ink firmly together with the fibers of the fabric. After the film has cooled, it must be peeled off the fabric, leaving the desired design pattern on the fabric.
Step 7 - Postpress
This is an optional step but highly recommended for best results and high-performance parameters such as wash and crock fastness. In this step, the final fabric with the transferred pattern is pressed in a heat press for about 10 to 15 seconds.
The above describes the printing process of the DTF printers. If you want to buy a DTF printer or ink, please contact us.
FCOLOR is a professional custom inkjet printer and ink manufacturer with 12 years of experience. Our products include DTF printers, inkjet printers, PVC/ID cards, card printers, label printers; dye-sublimation/digital printing equipment and consumables, dye inks, pigment inks, sublimation inks, film inks, DTF printer inks, and ink cartridges. We also provide customized solutions to our customers.